Bolzenschweißen
Beim Bolzenschweißen wird mittels Lichtbogenpressschweißung ein Schweißbolzen dauerhaft mit dem Werkstück verbunden.
Informationen zum Bolzenschweißen von Blech
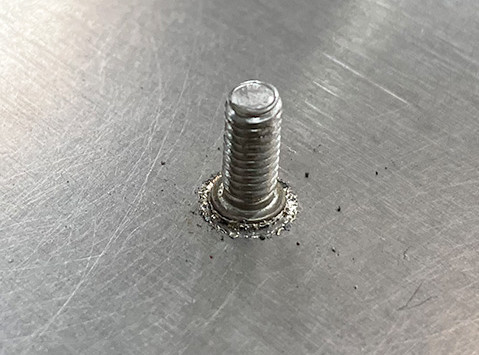
Das Bolzenschweißen ist eine Sonderform des Lichtbogenpressschweißverfahren. Es dient der Herstellung einer dauerhaften Verbindung von Normteilen (wie etwa Gewindebolzen, Stifte, Buchsen, Haken oder Ösen) mit größeren Bauteilen (Bleche oder Gehäuse). Hierfür wird zwischen der Stirnfläche des Bolzens/der Mutter und dem Werkstück ein Lichtbogen gezündet, wodurch beide Teile lokal aufgeschmolzen und anschließend unter geringem Anpressdruck zusammengefügt werden. Dieses Verfahren ist sehr zeitsparend und durch die vollflächige Verbindung wird eine sehr hohe Festigkeit erreicht.
Das Bolzenschweißen kann für runde, aber auch rechteckige Querschnittsformen verwendet werden. Neben den vielfach verwendeten und in der DIN EN ISO 13918 genormten Bolzen finden sich in den unterschiedlichen metallverarbeitenden Branchen eine große Anzahl von Schweißelementen nach kundenspezifischen oder Werksnormen.
Schweißelemente
Folgende Schweißelemente stehen zur Auswahl:
Gewindebolzen Vollgewinde | Edelstahl | M3 - M8 in verschiedenen Längen |
---|---|---|
Gewindebolzen Vollgewinde | Stahl verkupfert | M3 - M8 in verschiedenen Längen |
Gewindebolzen Innengewinde | Edelstahl | M3 - M6 in verschiedenen Längen |
Gewindebolzen Innengewinde | Stahl verkupfert | M4 in verschiedenen Längen |
Wie funktioniert das Bolzenschweißen?
Lichtbogenbolzenschweißen wird allgemein in Spitzenzündungs- und Hubzündungs-Bolzenschweißen unterteilt. Die beiden Methoden sind grundlegend identisch, unterscheiden sich lediglich nur in der Zündungsart des Lichtbogens.
Spitzenzündungsbolzenschweißen
Bei diesem Verfahren muss der Bolzen an der Unterseite eine kleine Spitze haben, die sog. Zündspitze. Hier zündet dann der Lichtbogen explosionsartig und schmilzt die gesamte Unterseite des Bolzens auf. Im geschmolzenen Zustand werden die beiden Teile dann dauerhaft miteinander verbunden. Da der Schmelzzustand vor allem bei dünneren Blechstärken ab 0,6 mm sehr schnell erreicht wird, ist die Spitzenzündung eine recht zügige Methode. Die Schweißbolze weisen in der Regel Durchmesser zwischen 2 und 10 mm auf. Diese spezielle Methode des Bolzenschweißen ist sehr variabel und vielseitig einsetzbar. In der Elektroindustrie und im Apparate- und Gehäusebau ist sie nicht wegzudenken.
Hubzündungsbolzenschweißen
Beim Hubzündungsverfahren liegt der Bolzen zu Beginn direkt auf dem Werkstück auf. Im Moment des Anhebens wird zwischen der Stirnfläche des Bolzens und der Oberfläche des Bauteils ein Lichtbogen gezündet. So entsteht an beiden Teilen eine lokale Schmelze, die dann unter geringem Druck zusammengefügt wird.
Das Hubzündungsschweißen ist die präferierte Methode, wenn dickere Bleche ab circa 2 mm Verwendung finden sollen. Als Schweißbolzen kommen Teile mit einem Durchmesser von 2 bis 22 mm (M24) zum Einsatz. Diese Blechstärken kommen vor allem im Stahl-, Maschinen- und Kesselbau zum Einsatz. Aber auch beim Schiffsbau ist das Hubzündungsbolzenschweißen meist das Mittel der Wahl.
Wo wird Bolzenschweißen eingesetzt?
Bolzenschweißen ist seit Jahrzehnten bewährt und findet regelmäßige Anwendung im Metallbau und der metallverarbeitenden Industrie. Mit dieser kostengünstigen Methode werden vornehmlich Gewindebolzen, Innengewindebuchsen oder Stifte dauerhaft mit anderen Bauteilen verschweißt. Die Verbindungen sind dabei in der Regel unsichtbar.
Zahlreiche Großindustrien wie z.B. Stahl-, Brücken-, Verbund- und Fassadenbau sowie Kraftwerks- und Industrieofenbau setzen dieses Verfahren tagtäglich ein.
Im Fahrzeug- und Schiffsbau sowie im Kessel- und Anlagenbau ist das Bolzenschweißen ebenfalls nicht wegzudenken.
Typische Anwendungsbereiche im Metallbau
Ist Bolzenschweißen einfach?
Bei dieser Schweißtechnik wird in der Regel kein “Schweißer” benötigt, sondern lediglich jemand, der die Geräte “bedient”. Da der Bediener im Gegensatz zum Elektroden-Hand oder MSG-Schweißen keinen Einfluss auf den Schweißvorgang nimmt, ist es leicht zu beherrschen.
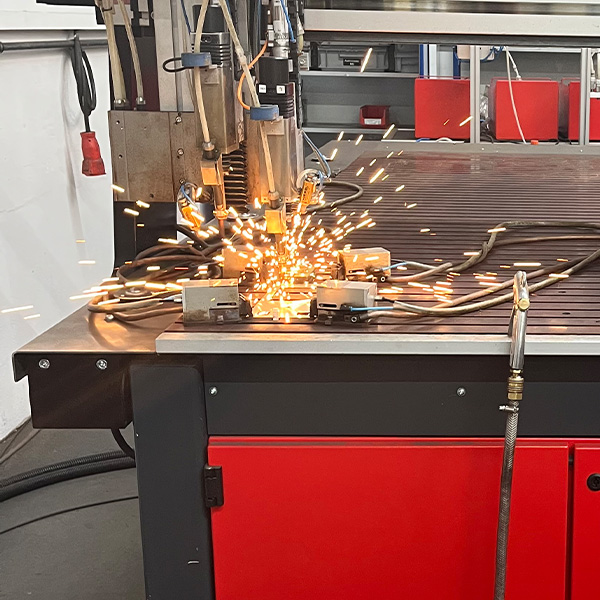
Dennoch erfordert die Auswahl des richtigen Verfahrens und die Bedienung der hochmodernen Anlagen ein großes Maß an Erfahrung und ein fundiertes Wissen über Materialeigenschaften sowie Vor- bzw. Nachteile der einzelnen Schweißmethoden.
Das Ziel einer möglichst hohen oder zumindest ausreichenden Fügequalität wird von zahlreichen Parametern beeinflusst. Die handwerkliche Geschicklichkeit und die fundierte Ausbildung des Bedieners sind entscheidende Größen. Erfahrung ist vor allem bei der Berücksichtigung der Schweißaufgabe und den damit verbundenen Anforderungen essentiell. Ein einwandfreier Prozessablauf legt darüber hinaus den Grundstein für ein optimales Ergebnis.
Welche Verfahren stehen zur Verfügung? Ein Überblick
In Abhängigkeit der Wärmeeinbringung haben sich verschiedene Verfahren und Prozessvarianten mit unterschiedlicher Bedeutung entwickelt.
Grundsätzlich lassen sich Bolzenschweißen mit Spitzen- oder Hubzündung nach der Art der Lichtbogenzündung unterscheiden. Die Verfahren ähneln sich natürlich, die Zündgeometrie der Bolzen ist jedoch grundverschieden. Aber auch der generelle Verfahrensablauf, die Gerätetechnik und die Anwendungsgebiete sind teilweise unterschiedlich. Während beide Techniken Gleichstrom verwenden, kommen doch verschiedenartige Energiequellen zum Einsatz.
Festigkeit der Verbindung
Wenn die Schweißung fachlich sauber und sorgfältig ausgeführt wurde, kann die Schweißverbindung eine größere statische Beanspruchung ertragen, als der Bolzen oder das Bauteil selbst. In Versuchsreihen wurde festgestellt, dass ein Bruch bei Überschreitung der Belastungsgrenze außerhalb der Schweißzone erfolgt.
Im Rahmen einer Festigkeitsberechnung sind vor allem die charakteristischen Werte von Bolzen und Blech ausschlaggebend, die Belastungswerte der Schweißung haben rechnerisch keinen Einfluss auf das Ergebnis.
Um die Bruchkraft zu berechnen, ist die Mindestzugfestigkeit der Werkstoffe entscheidend. Wenn Bolzenschweißverbindungen berechnet werden sollen, muss nach Einzelfall unterschieden werden. Das geltende Regelwerk sieht folgende Unterscheidungen vor:
- statische oder dynamische Beanspruchungen
- Druck, Zug, Biegung oder Torsion
Die Wahl der Bolzen hat daher so zu erfolgen, dass die Gebrauchstauglichkeit und Tragsicherheit des gesamten Bauteils gewährleistet ist. Die geometrische Ausprägung außerhalb der Schweißebene sowie die Bolzenlänge haben für den Schweißvorgang keine Bedeutung.
Die erforderliche Schweißgeometrie bzw. Bolzenspitze richtet sich nach dem jeweiligen Schweißverfahren. Bei einer längeren Schweißzeit, was zu einem längeren Anschmelzvolumen führt, muss die Bolzenspitze kegeliger sein. Daraus folgt, dass der Zündkegel bei Schweißelementen für die Spitzenzündung deutlich flacher ist, als bei einer Hubzündung.
Welche Bolzendurchmesser und -längen können verschweißt werden?
bei der Spitzenzündung | M3 – M8 | Ø3 bis 8 mm |
---|---|---|
bei der Kurzzeit-Hubzündung | M5 – M10 | Ø5 bis 10 mm |
bei der Hubzündung | M6 – M24 | Ø6 bis 25 mm |
Die Wahl der Bolzenlänge hängt von folgenden Kriterien ab:
Minimale Bolzenlänge:
Die minimale Bolzenlänge hängt von der erforderlichen Einstecktiefe zur ausreichenden Fixierung des Bolzens im Bolzenhalter ab. Dazu kommt dann noch der notwendige Überstand für die Bildung einer Schweißwulst sowie eine Sicherheitstoleranz, die abhängig vom Werkstoff und Durchmesser ist.
Maximale Bolzenlänge:
Theoretisch könnte die Bolzenlänge unbegrenzt sein, hängt aber natürlich von der verwendeten Ausrüstung ab. Der zu verschweißende Bolzen muss vom Stativ ausreichend abgestützt werden und die Pistole muss das (höhere) Bolzengewicht sicher bewegen können.
Verhältnis Bolzenlänge zu Bolzendurchmesser:
Ein Drehen des Bolzens während der Vereinzelung oder Zuführung sollte tunlichst vermieden werden. Aus diesem Grund muss vor allem bei Applikationen, die eine automatische Vereinzelung und Zuführung verlangen, das Verhältnis Bolzendurchmesser bzw. Flanschdurchmesser zu Bolzenlänge nicht 1:1 sein.
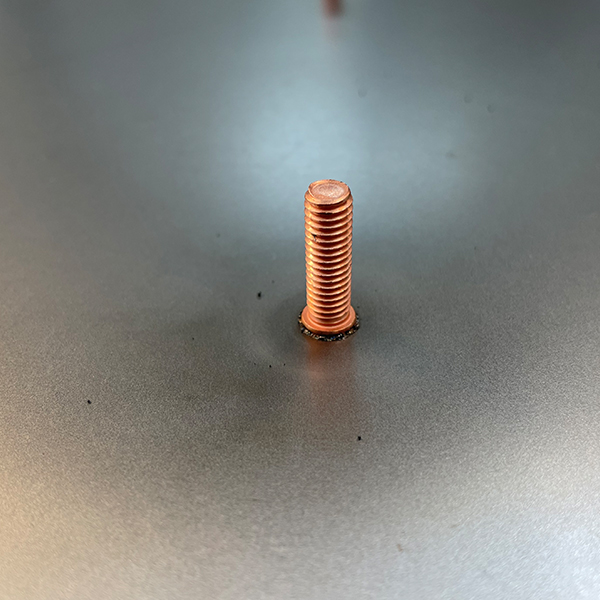
Welche Materialien oder Werkstoffe können verschweißt werden?
Prinzipiell sollten immer artgleiche Materialien verschweißt werden. Hier gibt es demnach keinen Unterschied zum konventionellen Lichtbogenschweißen.
Da beim Bolzenschweißen die Temperaturanstiegs- und Abkühlverläufe sehr schnell erfolgen (Lichtbogenbrennzeit < 1s), besteht bei Stahl die Gefahr der Aufhärtung durch Versprödung. Der Kohlenstoffgehalt C der zu verschweißenden Werkstoffe (Bolzen und Grundwerkstoff) sollte daher < 0,17% betragen.
Welche Oberflächenbeschaffenheit sollte das Bauteil haben?
Die Werkstoffe müssen sauber und metallisch blank sein.
Insbesondere an den Kontaktstellen – Bolzen zu Bauteil sowie Masseklemme zu Bauteil – muss die elektrische Leitfähigkeit uneingeschränkt gegeben sein.
Sollten Farbreste, Rost, Zunder, Fett bzw. Öl oder andere Schweiß ungeeignete Schichten (z.B. Eloxal) an den Bauteilen vorhanden sein, müssen diese rückstandslos von der Schweißstelle entfernt werden (mechanisch oder chemisch).
Eventuell vorhandene Oxidschichten bei Aluminium sollten ebenfalls entfernt werden.
Sehr kurze Schweißzeiten von unter 50 ms erfordern eine besonders sorgfältige Reinigung der Oberflächen.
Bei verzinkten Bauteiloberflächen muss im Vorfeld eine Prüfung auf Schweißbarkeit erfolgen.
Rückseitenmarkierungen
Verformungen bzw. Markierungen auf nichtrostendem Stahl oder Aluminium bis zu einer Blechdicke von 4 mm lassen sich selbst unter Einsatz der Spitzenzündung mit extrem kurzen Schweißzeiten kaum vermeiden.
Speziell bei hochglanzpolierten oder glanzlackierten Blechen ist die Sichtbarkeit zudem stark von der Rückseitenstruktur abhängig.
Im Blechdickenbereich von 0,6 mm tritt aufgrund der Schrumpfung des Schweißbades immer ein thermisch bedingter Einzug auf.
Rückseitenmarkierungen, wie beispielsweise Anlauffarben, kommen bei der Spitzenzündung deutlich weniger vor als bei der Hubzündung. Das liegt vornehmlich an den deutlich längeren Schweißzeiten der Hubzündung.
Die Stärke der optischen Beeinträchtigung hängt hierbei vor allem von der Materialdicke, der Metallart sowohl des Grundmaterials als auch des Bolzens ab und dem damit notwendigen Energieeintrag zur ordnungsgemäßen Verbindung.
Rückseitenmarkierungen lassen sich oft nicht vermeiden und sind kein Grund zur Beanstandung.
Profitieren Sie von unseren perfekt ausgebildeten Mitarbeitern und unserem hochmodernen Maschinenpark über den gesamten Prozess hinweg, von der Konstruktion bis zum fertigen Werkstück. Bei Fragen rund ums Bolzenschweißen stehen Ihnen unsere fachkundigen Berater jederzeit gerne zur Seite.